
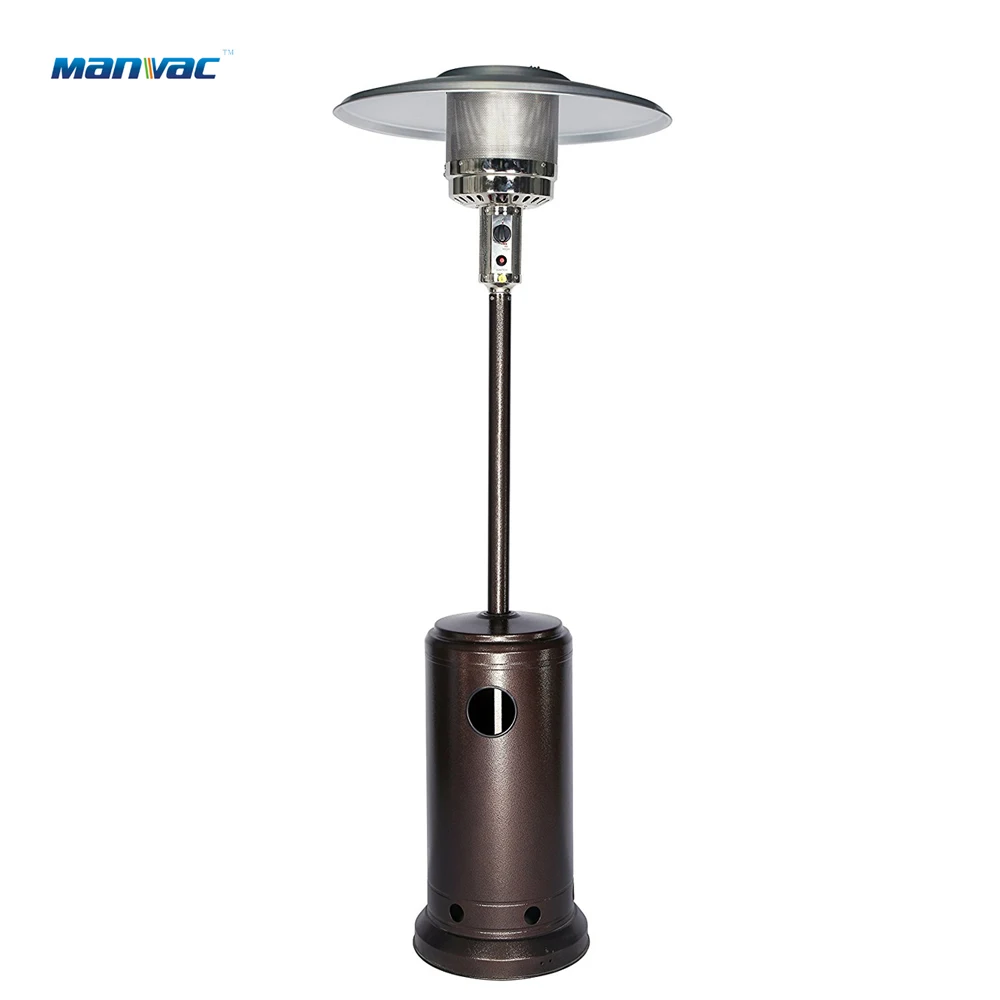
In the same type building heated with an infrared system, the temperature is much more uniform and the loft or roof area usually will be at a slightly lower temperature than the floor level… a good condition for minimizing heat loss. The ceiling area of a high bay building using a forced air system can be easily 30° to 40° warmer than the floor area. It literally acts as a heat sink, draining heat from the air and from personnel standing on the floor. The storage of the heat in the slab floor creates a low temperature emitter and a faster recovery time when large overhead doors are opened and closed.With a forced air system, the hot air rises to the ceiling and stratifies, gradually working its way down to thermostat level so that the floor slab never becomes warm enough to be comfortable. Infrared heats the floor slab, the machinery and the people first and then the air by using all three methods of heat transfer: radiation, conduction and convection. The major difference between a gas-fired infrared heating system and a forced hot air heating system is the method used to create a comfortable temperature. You may never know it is there, but it provides peace of mind. If heat levels increase due to heat exchanger failure, the wire melts and the safety circuit is broken, breaking the 24 volt circuit and shutting down the heater. Low voltage is then continuously passed along the wire in line with the gas control circuit. The revolutionary TISS™ uses a simple principle to place an electrically insulated aluminum wire in tension above the reflector. In the unlikely event of a tube failure, TISS™ has been designed to automatically shut off the heater. SunStar’s patent pending innovative safety feature for positive pressure radiant tube heaters is called the “Tube Integrity Safety System” (TISS™). Introducing TISS™ Tube Integrity Safety Shut-Off System Suitable for horizontal or angle mounting up to 45°.Optional aluminized steel radiant tubes (Tough Guy Option).Standard highly emissive radiant tubes (10’ lengths).heat treated aluminized steel combustion chamber (10’ length) Step-opening redundant combination gas valve for quite ignition and added safety.Diaphragm air switch for proof of venting before gas flow and ignition.30 second pre-purge before ignition and 30 second post-purge after thermostat is satisfied.Heavy duty permanently lubricated ball bearing, totally enclosed motor for maintenance-free operation.Ideal for applications where minimal noise (less than 60 dB) is desired. Blower motor totally enclosed in the burner box.No draft hoods, totally enclosed combustion chamber.Products of combustion are pushed through the combustion chamber.
